Everywhere you look, it’s obvious: Devices today are getting smaller. What you may not realize is how small they’re truly becoming.
Enter microelectromechanical systems (MEMS). MEMS are tiny devices or systems with both electrical and mechanical components. These systems range from a few micrometers to a few millimeters in size. At these scales, there is little room for error, which makes MEMS characterization and testing one of the most important steps in the design process of such systems. Let’s break MEMS down a bit more:
- Micro: These devices are on the microscale.
- Electro: These devices contain electrical components like sensors.
- Mechanical: These devices contain mechanical components like actuators.1
How to perform MEMS characterization
It’s difficult to get any two MEMS devices to behave the same way. The devices are challenging to test due to their size, and performance inconsistencies are common. This reality can make figuring out what tests to run and how to run them daunting. To fully test your MEMS device, you’ll need to assess performance, reliability, and functionality. Let’s go over a few instruments you’ll need to get started, and several tests to consider when performing MEMS characterization.
Equipment needed for MEMs characterization
- Arbitrary Waveform Generator and Waveform Generator to generate an input signal with respect to the device under test (DUT)
- Oscilloscope and Spectrum Analyzer to measure the output of the DUT in the time and frequency domains
- Lock-in Amplifier to extract signal information if the device has a poor SNR, or signal-to-noise ratio (Figure 1)
- Frequency Response Analyzer for frequency response analysis
- Digital Filter Box for filtering excess noise/signal preemphasis
- PID Controller for feedback control and stability
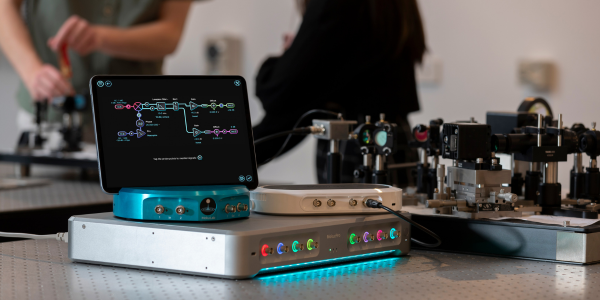
Figure 1: Use the FPGA-based Moku Lock-in Amplifier for fast, flexible extraction of critical signal information if your MEMS device has a poor SNR.
Tests to run
Response time: Measure how quickly the device can react to changes in the environment
Instruments needed: Waveform Generator, Oscilloscope
- Establish the device baseline output without changing the input.
- Apply a step input signal to the DUT.
- Note: The type of signal depends on the type of DUT. Feel free to use a different signal.
- Record the response of the device until it reaches a steady-state.
- Measure the time it took the device to transition from the baseline state to the response from the step input, or 10-90% of the final value.
- Repeat this measurement under different operating conditions.
Frequency response: Measure how the device behaves at different frequencies
Instruments needed: Frequency Response Analyzer, Digital Filter Box
- Set up a Multi-instrument Mode configuration with a Digital Filter Box (for filtering and amplification) and Frequency Response Analyzer.
- Perform a frequency sweep to measure the amplitude of the MEMs device’s response at each frequency. Look at the phase shift introduced by the device at different frequencies.
- Identify the resonance frequency, where the MEMS device exhibits the highest response.
- Calculate the 3 dB cutoff frequency/bandwidth of the device to identify the operating range of the device.
- Check for distortion and nonlinearities.
- Perform this test under different environmental and temperature conditions.
Calibrating your MEMS device
Instruments needed: Waveform Generator, Data Logger, Oscilloscope or Spectrum Analyzer
- Use a trusted, stable source to generate a known signal.
- Measure the response of the DUT to the known signal.
- Record the results using a Data Logger.
- Establish a relationship between the input and output, or a calibration curve.
- Determine correction coefficients based on this curve. Apply these to the DUT and repeat measurements.
Measure noise: Analyze how well the DUT can maintain a strong signal relative to the noise level
Instruments needed: Arbitrary Waveform Generator or Waveform Generator, Spectrum Analyzer, Oscilloscope
- Record baseline noise floor with no input signal.
- Apply a known, stable input signal.
- View the result on the Spectrum Analyzer.
- Measure amplitude of signal and any interference/noise.
- Measure the noise power background in a frequency band far from the signal.
- Calculate SNR in dB with
, signal power and noise power are in units of power such as watts (W).
Measure mean time between failures (MTBF) to measure device reliability
Instruments needed: Data Logger, Spectrum Analyzer, Oscilloscope
- Define what the failure events include: hardware failures or software failures?
- Operate the device over a defined period of time and record the number of failures.
- Calculate the MTBF for each type of failure:
- Keep an eye on the failure rate over time for the most meaningful data.
Examples of MEMS devices
MEMS devices are important in a range of applications, from actuators to automotive.
Sensors
- Accelerometers that detect motion in smartphones
- Gyroscopes that detect rotation in cameras for image stabilization
Actuators
- Small valves that respond to electrical stimulation with movement, such as in microfluidics
- Piezoelectric actuators used in autofocus in cameras, precision positioning systems, and even inkjet printer nozzles
Optics
- Optical MEMs devices like micro-mirrors and micro-lenses in optical switches and adaptive optics, including micro-electrothermal actuators (META)
- Variable optical attenuators (VOAs) to adjust the intensity of light signals in fiber-optic communications
- MEMs-based beam steering to control the direction of a laser beam in LiDAR or free-space optical communications (FSOC)
Biotechnology2
- Microneedle arrays for minimally invasive drug delivery and biosensing
- Pressure sensing such as MEMS-based blood pressure monitors
- Micro-optical coherence tomography (µOCT) that provide high-resolution, cross-sectional imaging of biological tissues
Automotive3
- Accelerometers that measure changes in speed
- Tire pressure monitoring systems (TPMS)
- Inertial measurement units (IMUs) for advanced driver assistance systems (ADAS) and autonomous vehicles
Conclusion
MEMS technology continues to permeate across multiple industries, including optics and photonics, biotechnology, and more. Researchers are taking advantage of the attractive features of MEMS devices, integrating them into more compact and portable devices than ever before. Since these devices are still emerging and undergoing significant research, proper testing and characterization are critical in order to identify how we can improve them.
Modern, software-defined instruments provide a fast, flexible solution for MEMS testing. For example, researchers at Oregon State University are using the Moku platform to design a low-noise system containing an end-to-end prototype in a single device. To learn more, check out our case study.
Questions?
Get answers to FAQs in our Knowledge Base
If you have a question about a device feature or instrument function, check out our extensive Knowledge Base to find the answers you’re looking for. You can also quickly see popular articles and refine your search by product or topic.
Join our User Forum to stay connected
Want to request a new feature? Have a support tip to share? From use case examples to new feature announcements and more, the User Forum is your one-stop shop for product updates, as well as connection to Liquid Instruments and our global user community.
[2] Chircov, Cristina, and Alexandru Mihai Grumezescu. “Microelectromechanical Systems (MEMS) for Biomedical Applications.” Micromachines, vol. 13, no. 2, 22 Jan. 2022, p. 164, https://doi.org/10.3390/mi13020164.
[3] “MEMS automotive sensors drive the future of mobility,”Atomica, Jul. 29, 2020. https://atomica.com/mems-automotive-sensors-drive-the-future-of-mobility/#:~:text=These%20sensors%20are%20the%20dominant