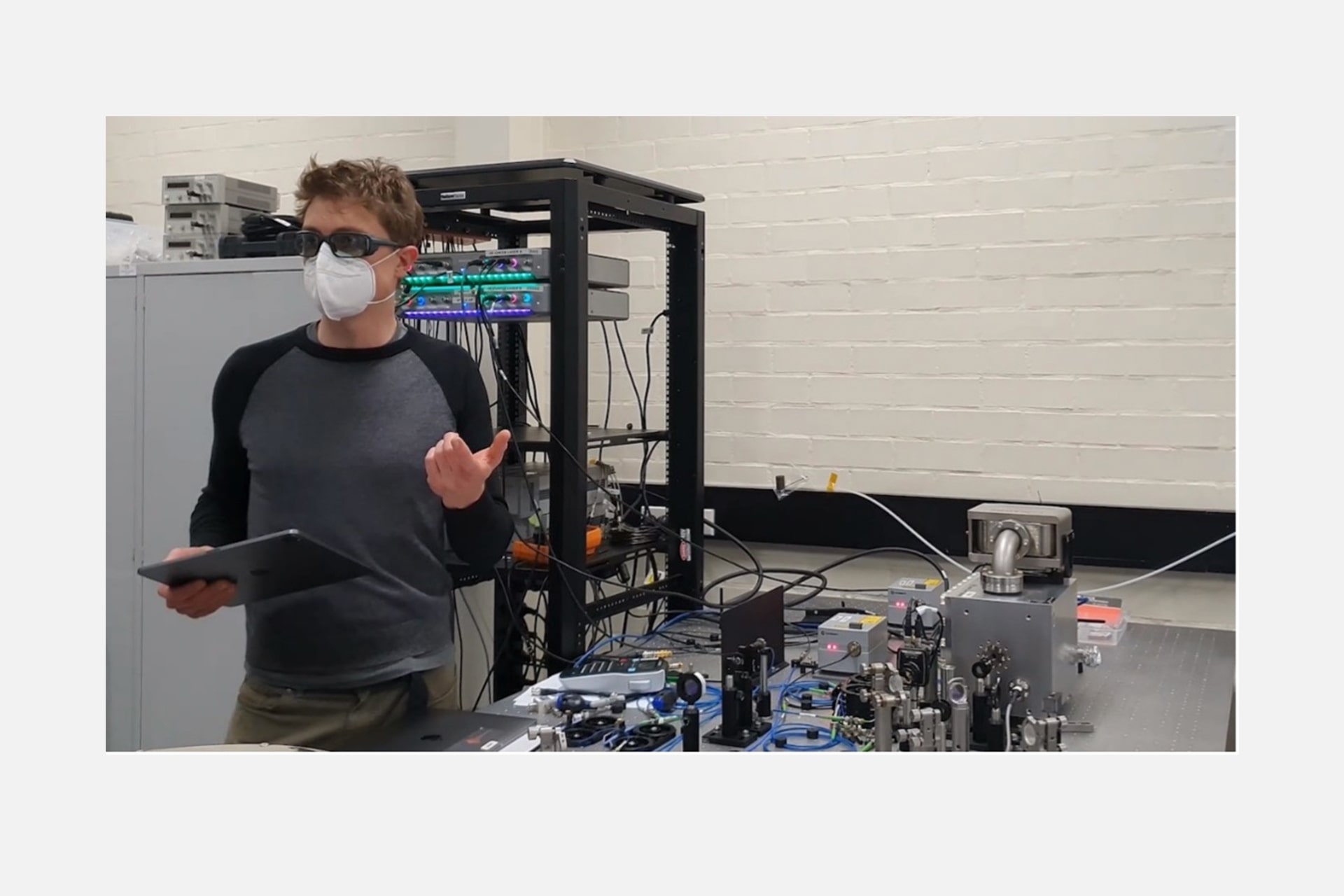
Summary
At the Centre for Gravitational Astrophysics/OzGrav at the Australian National University, Dr. Andrew Wade and team are developing ultra-stable frequency reference sources for use in long-range, high-precision laser sensing projects. Moku:Pro’s Laser Lock Box and its FPGA-based digital implementation enables them to easily acquire lock and tune parameters for a more accessible, robust solution compared to their previous custom setup.
Challenge
In their work to develop space-based laser sensing technology, researchers at ANU rely on very precise measurement and control of laser frequency. When using a laser to measure across long distances, for example between satellites in orbit, even a small change in the laser’s frequency introduces significant uncertainty or noise into the measurement. Determining the frequency of a laser and suppressing fluctuations in that frequency over time are key to the research at ANU. An additional challenge is that the custom nature of each laser and frequency reference (cavity) means that the control system must be tailored to each setup.
According to Dr. Wade, “Analog circuits have some advantages in bandwidth and loop latency, but typically are more susceptible to offsets, environmentally induced drift, and spurious cross couplings. There is also the problem of how to acquire lock and tune loop parameters which is often done through a manual process: physically flicking switches and tuning with front panel knobs.” With a very limited selection of laser locking devices on the market, most laboratories resort to building their own for performance reasons, incurring significant overhead in building and maintaining these setups.
Figure 1: ANU lab setup locking a laser to a 100,000 finesse reference cavity
Dr. Wade and his team are using the highest finesse cavity commercially available which presents further challenges. The extremely narrow resonance of the 100,000 finesse cavity means that the linear capture range of the Pound-Drever-Hall (PDH) error signal is very small, making it difficult to acquire lock.
Solution
The digital implementation of Moku:Pro’s Laser Lock Box addresses many of the short-comings of the analog circuit design approach. The FPGA-based architecture allows for reconfigurability to adjust for different lasers or references, while real-time parameter tuning and visualization of error and control signals make the process of optimizing the loop design much more straightforward.
As an integrated cavity locking unit, Moku:Pro is able to provide an intuitive user interface that makes locking and tuning the feedback controller much more accessible, while reducing complexity and possible points of failure. “Debugging broken wires and soldering fixes to PCBs seem to be a thing of the past now,” said Dr. Wade. “All the elements of digitization, demodulation, frequency shaping, and blending of actuators are done in a single unit making it fast to install and get up and running.”
Figure 2: Laser Lock Box iPad interface block diagram and intermediate probe points showing the error and control signals
Utilizing Multi-Instrument Mode on Moku:Pro, they are able to lock their lasers to optical cavities with the Laser Lock Box while also making Bode plot measurements with the Frequency Response Analyzer (FRA) with no additional test equipment or wiring. The FRA injects a disturbance into the error signal to measure the transfer function of the system, providing a check of closed loop gain and phase margin as well as the loop’s disturbance rejection performance. Researchers can quickly switch between the FRA and Laser Lock Box to adjust PID parameters to optimize loop performance to ensure stability and maximize disturbance suppression.
Figure 3: Researcher measures the control loop phase margin on a Bode plot using the Frequency Response Analyzer in Multi-Instrument Mode
Upon feedback from ANU to Liquid Instruments, a demodulation-free input was also added to the Laser Lock Box enabling them to implement a custom laser-cavity readout scheme using Moku:Pro’s standard instrument suite. This new feature allowed them to avoid building their own custom system and saved a significant amount of time, highlighting the benefits of Moku:Pro’s software-defined approach.
After gathering data on the frequency stability and loop characteristics, researchers save and export it for documentation, publication, and offline modeling. Moku:Pro’s Wi-Fi connectivity ensures that this can be done remotely and quickly. Laser frequency stability data can be continuously recorded over very long log times, limited only by the size of the storage.
Result
With Moku:Pro’s combination of capability and flexibility, ANU was able to get up and running quickly, avoiding the overhead of building and maintaining a custom system. “Switching to Moku:Pro for laser locking saved a lot of time in set-up and the intuitive user interface makes tuning parameters much more straightforward,” said Dr. Wade. The reconfigurability and upgradability of the solution ensures it can be adapted to new experiments as they continue their research into space-based laser sensing technology.
Have questions or want a printable version?
Please contact us at support@liquidinstruments.com