Introduction
Microelectromechanical systems (MEMS) are minuscule but mighty machines, typically ranging from a few micrometers to a few millimeters in size. These tiny workhorses can sense, control, and manipulate their environment at a very small scale. Researchers use them in a range of applications, from sensors to actuators to microfluidics. To ensure their reliability, these devices require extensive testing in a variety of environments, such as testing in a vacuum, verifying performance at different temperatures, and confirming material properties like weight and stiffness. These varying test environments and parameters can be difficult for researchers to achieve or simulate.
A team of researchers led by associate professor Jason Clark of Oregon State University has patented a new force-feedback technology that increases or decreases the effective mass, damping, or stiffness of MEMS devices. Using Moku:Go for feedback control, Jason’s team is working to demonstrate new methodologies for testing MEMS devices like gyroscopes to streamline and enhance MEMS design.
Moku:Go (Figure 1) is the most versatile and affordable test hardware in its class. This powerful, FPGA-based solution offers 15+ software-defined instruments in a single device, from quintessential engineering tools like an Oscilloscope to advanced instruments like the Laser Lock Box. The wide array of easy-to-use instruments enables researchers to achieve more, faster, in settings ranging from optics labs to industry R&D facilities.
Users can switch between instruments seamlessly to optimize their Moku:Go to the tasks at hand. And with Multi-Instrument Mode, users can combine pairs of instruments, like the Lock-in Amplifier and PID Controller, to run simultaneously with lossless interconnection.
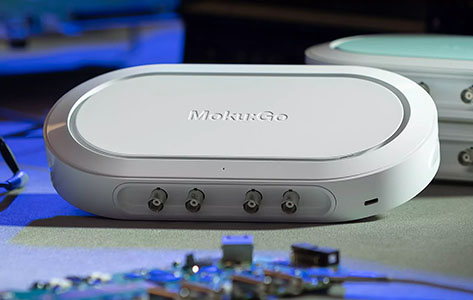
Figure 1: Moku:Go, a compact, versatile device including 12+ software-defined instruments
The challenge
Historically, researchers have struggled to coax any two MEMS devices to behave identically. They have tried testing MEMS in a vacuum to achieve a higher resonant frequency, a process that is incredibly expensive and impractical even for the world’s most advanced laboratories. Like Jason and his team, many companies and researchers are now attempting to counteract process variations in MEMS manufacturing that lead to performance inconsistencies. For example, there may be many MEMS devices on a wafer (Figure 2). Even if they’re all meant to resonate at 30 kHz, none of them will successfully resonate at the desired frequency due to process variations in geometry and material properties. In their pioneering research, Jason and his team are using Moku:Go and their force-feedback technology to account for these process variations and force the resonators to resonate at the desired frequency.

Figure 2: Left: Resonators before researchers apply force-feedback technology. Right: Resonators after researchers apply force-feedback technology, achieving the desired resonant frequency
Before selecting Moku:Go, the researchers considered other solutions to create this patented technology, but they found that other FPGA tools were out of budget and not intuitive to use. In addition, the team spent more than three years adjusting analog components and designing circuitry to achieve their goals, but ran into extensive noise issues, halting progress. After purchasing various pieces of equipment to try to solve this issue and spending significant time troubleshooting to identify the source of the noise, the team turned to digital instrumentation. Moku:Go provided an ideal solution, effectively eliminating all analog noise by digitally processing their signals.
The solution
Using the Moku:Go PID Controller as the feedback component, Jason’s team is working to prove that they can manipulate a 10 dollar gyroscope to behave like a 10,000 dollar gyroscope. Typically, high-performance gyroscopes increase in cost as the Q-factor, or quality factor, increases (Figure 3). However, by implementing reconfigurable, FPGA-based feedback systems, the team has shown that they no longer need to rely on expensive test environments, such as testing in a vacuum, to advance their research. With their force-feedback technique, a system could behave in air as it would in vacuum, potentially saving thousands of dollars.

Figure 3: Gyroscope vs. quality factor for popular gyroscope models
Using the flexibility of Multi-Instrument Mode for Moku:Go, researchers first enable the Lock-in Amplifier to lock to a desired frequency. Then, they seamlessly deploy a PID Controller for feedback control. The researchers then process the signal digitally and analyze the results, all within Moku:Go. By utilizing digital instrumentation, Jason and his team have eliminated their noise issue. They can also quickly and easily reconfigure their digital circuits by adjusting feedback parameters, changing filter corner frequencies, and troubleshooting using the embedded Oscilloscope.
“Going digital, Yingsong Han is really happy about this because one, he’s going to have much lower noise, and two, it’s easy to change,” said Jason of his graduate student’s success using Moku:Go. “If he wants to change something, we don’t have to buy anything new. He can just redo the setup virtually.”
The result
Thanks to the best-in-class performance of Moku:Go, the team can create custom digital signal processing circuitry, leading to groundbreaking discoveries in the MEMS testing field. By using nonlinear feedback from the Moku:Go PID Controller, they achieved unprecedented high-Q, large-bandwidth resonance behavior from inexpensive gyroscopes, seen in Figure 4.

Figure 4: Bandwidth vs. Q before feedback (blue) and after feedback (red)
Conclusion
With Moku:Go, Jason and his team have designed a low-noise system that offers an end-to-end prototype contained in a single device, all with minimal troubleshooting. By developing a cost-effective, highly efficient test environment for microelectromechanical systems, they have significantly advanced the MEMS research and design field. As Jason and his team continue to test and optimize their research and patented force-feedback technology, Moku:Go will help transform their designs from ideas to prototypes without any additional expensive instrumentation.
To learn more about Moku:Go, contact info@liquidinstruments.com.
To learn more about how Professor Clark is redefining engineering education with Moku:Go, check out his course, Automating the Future with Moku:Go, or listen to his exclusive webinar here.