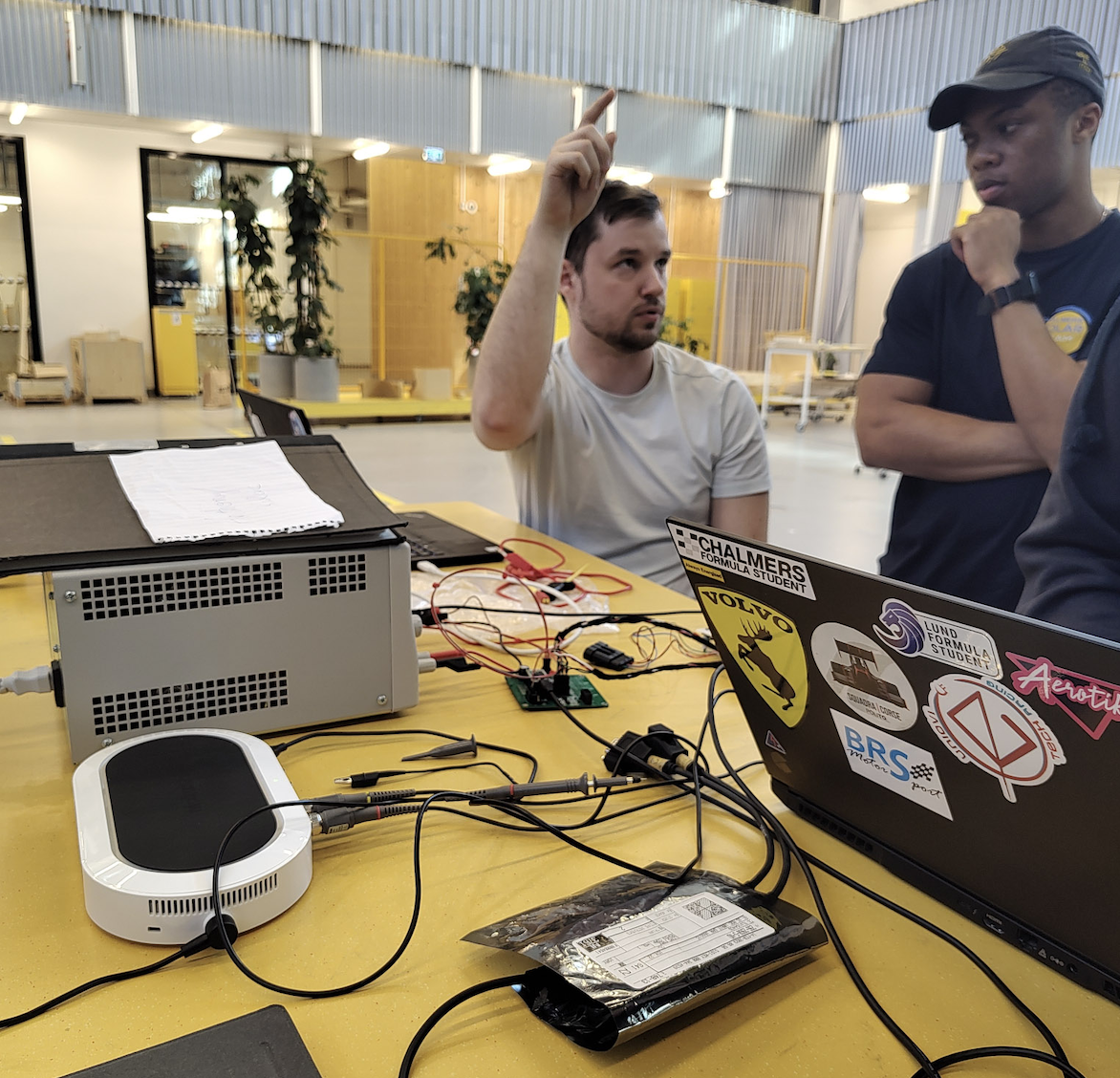
Introduction
Founded in 2018 in Gothenburg, Sweden, the Chalmers Solar Team is a student-driven, nonprofit project aiming to build competitive, sustainable solar-powered electric cars (Figure 1). The team competes in the Bridgestone World Solar Challenge, an annual event that attracts teams from leading universities around the globe to put their designs to the test in a grueling race through the Australian outback. With more than 40 members spanning across multiple focus areas, including aerodynamics, mechanics, electrical systems, and logistics, the team has made significant improvements to their car design this year. Viswanathan Ganesh, the lead electrical engineer on the project with a passion for renewable energy and sustainability, utilizes two Moku:Go devices for motor actuation, battery management system (BMS) testing, and drive tests.
Figure 1: Chalmers Solar Team members working with Moku:Go
Moku:Go is the first software-defined instrumentation solution from Liquid Instruments tailored for engineering education and general industry. The software-defined functionality enables Moku:Go to provide up to 15 different instruments used in electronics, optics, and telecommunications labs. With Multi-Instrument Mode (MiM), users can combine pairs of instruments to run simultaneously with lossless interconnection.
The challenge
This year, the Chalmers Solar Team approached their design with a sustainability-first mindset. To achieve their goals, they needed to redesign parts of their vehicle to reduce total weight, improve motor performance, and fine-tune components. On the electrical team, Viswanathan led his team members to develop new strategies and rework their BMS to achieve a more efficient, streamlined design.
Since most team members are students, they have to meet on weekends to test their designs. With limited time and lab space to perform testing, the team needed a portable, flexible solution. To perform in-vehicle drive tests, conventional benchtop equipment is simply not an option. Traditional oscilloscopes left the team members tethered to a benchtop, unable to log data efficiently, and prevented effective collaboration due to the unintuitive, difficult-to-read display and functionality. Different team members required different equipment and instruments to perform tests on the vehicle subsystems, so with legacy equipment, the team would have needed several costly benchtop instruments to complete their testing. This also would have included external data processing to review any logged data, further pushing the design timeline and delaying progress.
The solution
After testing Moku:Go on his own independent projects, Viswanathan selected the device for the Chalmers team. The compact design allows team members to bring an entire lab along in their backpack, and even connect Moku:Go to a portable power source to perform in-vehicle field testing.
“In the initial drive testing, we just connected the Moku:Go in the car and logged everything — voltages, currents — and then studied it,” said Viswanathan of the drive testing. “It was great.”
The ease of use allowed team members to share two Moku:Go devices for a variety of tests, eliminating the need for multiple benchtop instruments. To improve their BMS and solar cell strategy, the solar cell group uses one Moku:Go device to calculate voltage drop and voltage rise, ensuring the team is delivering maximum power to their vehicle. Depending on the voltage drop, the team can calculate their boost converter’s maximum power point tracking (MPPT) logic. Simultaneously, the motor control group uses the other Moku:Go device to calibrate the motor controller. They initiate the motor at different voltage levels, checking the resulting speed with a tachometer. With this data, the team then could calibrate the motor controller. Figure 2 shows the Moku:Go in use to test vehicle subsystems, conveniently displayed on a team member’s laptop.
Figure 3: The students use the Moku:Go Oscilloscope, one of 15 instruments, to perform various tests across teams
Finally, the battery group takes over, using both Moku:Go devices. This year, the team is splitting their design to include two battery packs to improve their center of gravity. With no specific battery datasheet, the team is calibrating their BMS and specifying their batteries on their own. They perform open-circuit voltage (OCV) testing with the Moku:Go Oscilloscope/Voltmeter to specify the electrical potential of the battery. They form an RC model of the battery, then begin testing charging and discharging cycles. They first perform these tests on a single cell before forming a string of cells, connecting them to the BMS, and repeating testing. They repeat this process until they have fully characterized the cell performance.
The result
The team significantly improved their car design by performing extensive, meticulous testing with Moku:Go. One of the most useful instruments, besides the Oscilloscope, was the embedded Data Logger.
“We don’t need to have any data logger separately,” said Viswanathan. “While running a sequence of tests, we can just mark the time period in which we are doing which test.”
The team simply connected their Moku:Go to an external power source to perform in-vehicle data collection for up to six hours and 23 minutes, providing crucial information on the performance of various subsystems.
Conclusion
The Chalmers Solar Team was able to fully redesign their vehicle with the help of Moku:Go, setting the team up for success for this year’s Bridgestone World Solar Challenge kicking off in Darwin, Australia.
To learn more about Moku:Go, contact info@liquidinstruments.com.